MPET, Europe’s largest container terminal located in Antwerp, equipped its 41 STS crane with Camco BoxCatcher OCR camera system for container identification and condition recording. The flying camera, hoovering on crane mounted rails, is linked with the crane PLC and captures every box, regardless the container flight path. Seamless TOS integration ensures that the captured data is instantly sent to the TOS, ultimately improving vessel turnaround time.
MPET: SINGLE LARGEST CONTAINER TERMINAL IN EUROPE
MPET operates Europe single largest container terminal located in the port of Antwerp. In 2015/2016, the MSC PSA European Terminal (MPET), a 50/50 joint venture between TIL and PSA, moved its operations from the Delwaidedock on the right bank of the river Scheldt to the Deurganckdock on the left bank. The terminal’s annual throughput capacity thus expanded to 9 million TEU. MPET now features a total of 41 quay cranes across 9 berths, 234 straddle carriers and a quay length of 3,700 meters, making it the single largest container handling facility in Europe.
41 QUAY CRANES FEAUTURING INTELLIGENT OCR/OFR CAMERAS
In 2018, Camco Technologies was awarded the contract for the supply, implementation and maintenance of BoxCatcher Crane OCR systems for 41 cranes. In only two years, all of the BoxCatcher equipped quay cranes were fully operational.
A DISRUPTIVE SOLUTION FOR STS CRANE AUTOMATION
In search of a robust OCR crane solution, MPET had been assessing different routes. A PTZ camera system seemed not a viable solution, fixed CCTV cameras were considered for a moment, but this solution would require a substantial set of cameras per crane to avoid blind spots, a complex system integration and possible significant downtime during camera maintenance. Moreover, lack of proven solutions in the container handling industry was an additional drawback. The risk assessment for both alternatives soon turned negative. With only two dynamic cameras per crane, Camco BoxCatcher system came out as the best STS crane automation solution. The Camco BoxCatcher disruptive design composed of a flying camera system hoovering over vertical rails fixed onto the crane frontal legs, enabling the capturing of every container, whatever the spreader flight path. With the Camco solution, only two BoxCatchers per crane are required for container identification providing 360° images of each box, be it 20, 40 or 45ft containers. Apart from increased performance, Camco STS crane solution contributes to more safety under the crane. Tallymen now let the crane OCR do the work and only focus on exceptions from a remote and safe office.
The BoxCatcher crane software application integrates seamlessly with the terminal TOS via the PSA middleware ConEqTer which serves as the tallyman exception portal. The primary OCR process with connection to the crane PLC is run by Camco.
PERFORMING AND RELIABLE TOS INTERFACES
The BoxCatcher connects to the crane PLC via a PC fitted in the e-house of the crane. When the spreader passes through the portal legs, the cameras make pictures automatically. The driver does not have to follow a fixed flight path but determines the best trajectory without having to worry about the OCR system. The pictures are instantly processed on the cameras and the generated data is interfaced via the COS – the Crane Operating System – with the terminal operating system. Harold states that “the TOS interfaces seamlessly with the COS and receives data from the cameras without delays. At the same time, the TOS feeds data to the Crane Operating System.”
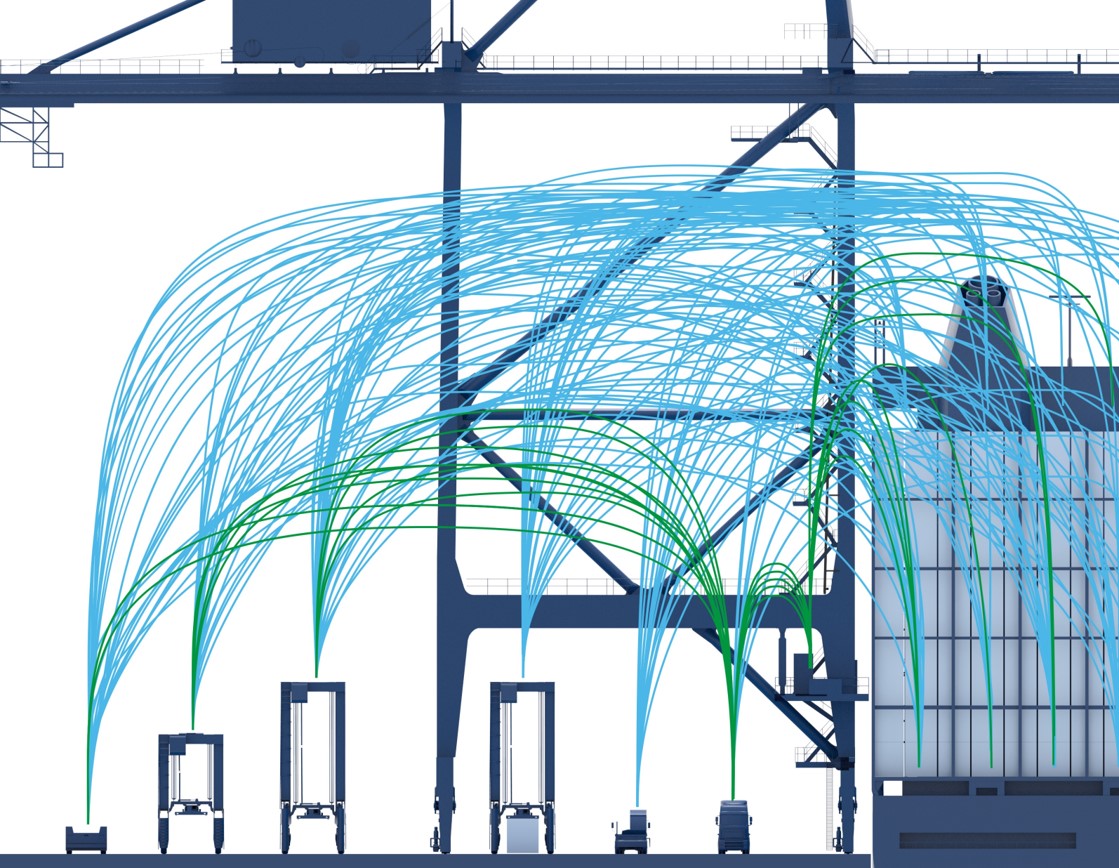
With the BoxCatcher linked to the crane PLC, the system predicts the precise location where the container will cross the frontal crane legs, avoiding unnessary moves for identification.
STREAMLINING THE TALLY PROCESS DURING LOADING AND DISCHARGE
The intelligent BoxCatcher cameras are equipped with OCR/OFR engines and partially take over the tallyman’s tasks. They capture images and data of each container while it’s loaded or discharged from the ship, without interrupting normal crane operations. The system reads the container number, ISO code, dangerous goods labels and checks for seal presence. At the same time, it takes high-resolution pictures for later damage claims management. Captured container data is then verified against the load lists. Waterside container handling is thus fully automated – human intervention is only needed in case of exceptions. To swiftly handle these exceptions, MPET uses Camco’s Crane Operator application.
ACCURACY OF INFORMATION
The sooner information is available, the sooner real-time planning processes can start. It goes without saying that the information needs to be accurate and reliable. For any terminal, it should be a target to put every box in the right position and not touch it again until it leaves the terminal. Accuracy of information is a key parameter to reduce planning errors, avoid rehandles, housekeeping or shifting moves and idle moves. Fewer moves mean less fuel consumption, less wear and tear of the handling equipment and a higher productivity rate on the yard.
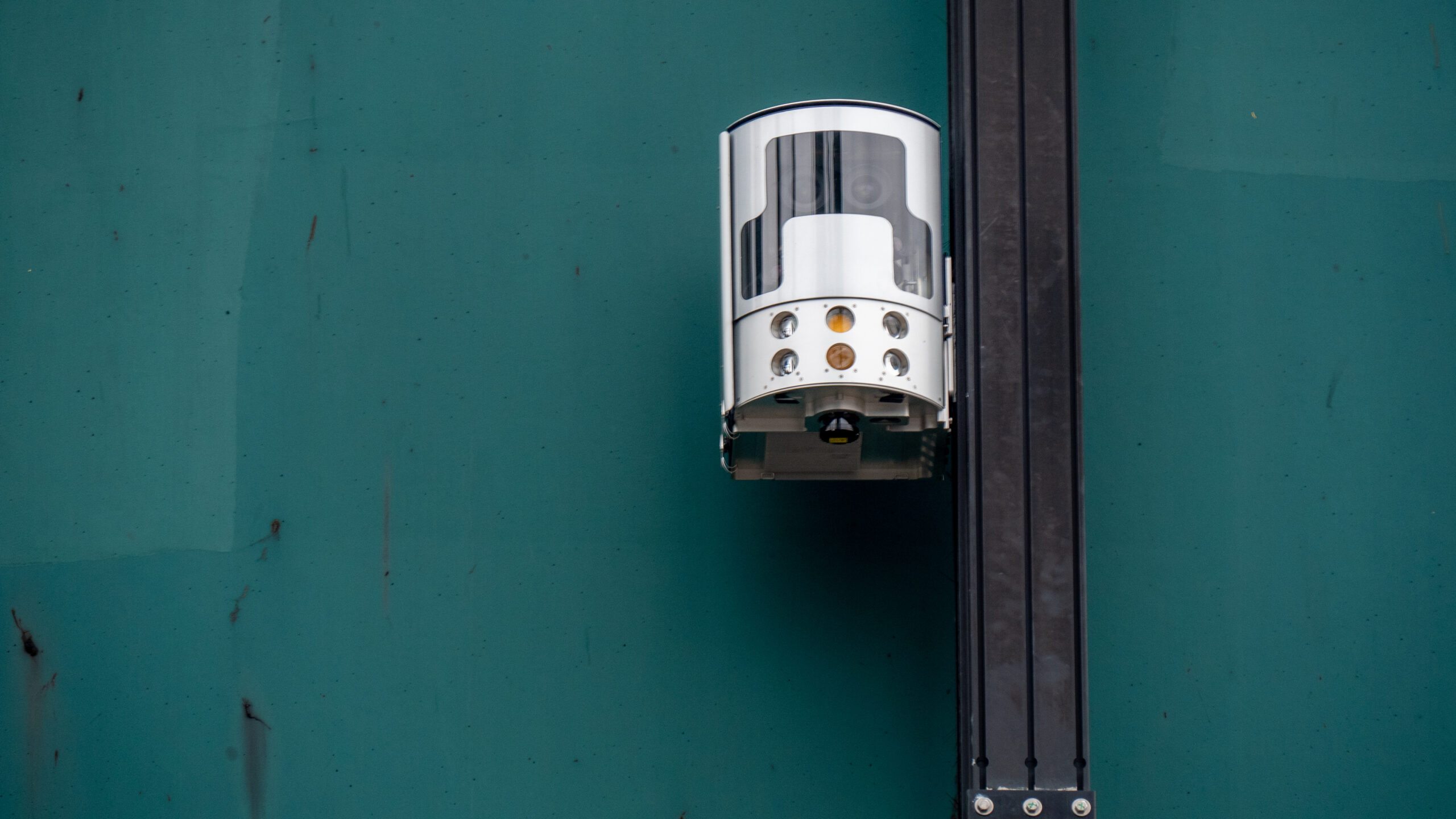
Per STS crane, 2 BoxCatchers hoover along the crane legs, capturing data as well as pictures of the container long and short sides.
COMMUNICATION AND CLOSE COLLABORATION
Implementing 41 cranes with two BoxCatcher systems per crane was quite a challenge. The joint project team was well prepared and had learned from an earlier Box-Catcher implementation project at PSA Antwerp. Each party focused on its expertise. Camco organized to have the 42-meter rails assembled beforehand on a dedicated warehouse on-site. Hoisting the rails took place in scheduled windows of 2 by 2 cranes. This way, Camco and MPET managed to install and commission two cranes in just a 2-3-day time window.
Aware of the many challenges, the MPET team succeeded well in taking into account all aspects of the operation without disrupting operations:
- maximum preparation of the cranes during normal maintenance windows: cabling, electrical cabinets, industrial PCs, IT network testing etc.
- detailed planning of installation weeks: hoisting, fiber cable pulling
- relying on the in-house partner for STS welding works for greater efficiency
- avoiding aerial/boom lifts and relying on specialized STS crane climbing team
- getting stakeholders on-board with an extensive training and communication roll-out
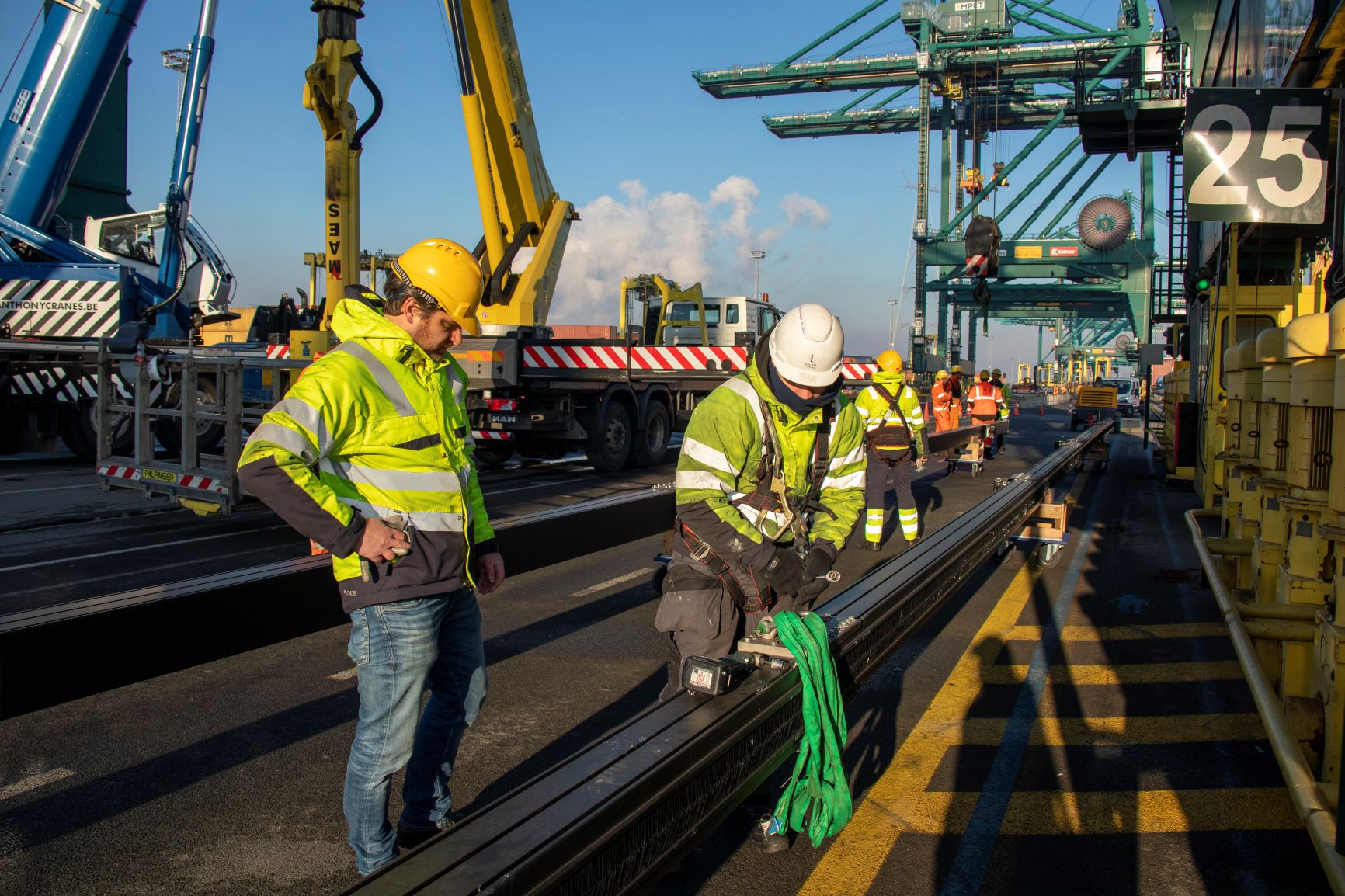
Hoisting the rails onto the cranes. Every 2 to 3 days, 2 cranes were equipped with 2 BoxCatcher per crane.
FROM DESIGN TO INSTALLATION IN JUST 12 MONTHS
“With 82 BoxCatcher installed on 41 cranes in less than one year, and minimal operational impact in a record year of handling 7.5+ million TEU in Europe’s single largest container terminal with the biggest crane density, this project has been very successful to say the least”.
Short communication lines between the MPET and Camco project team contributed to its success. Of course, as with every similar scale project, it’s easy to pinpoint improvements after implementation or call for earlier issue identification avoiding unnecessary surprises underway. But then, project business is project business and the unexpected never far away.
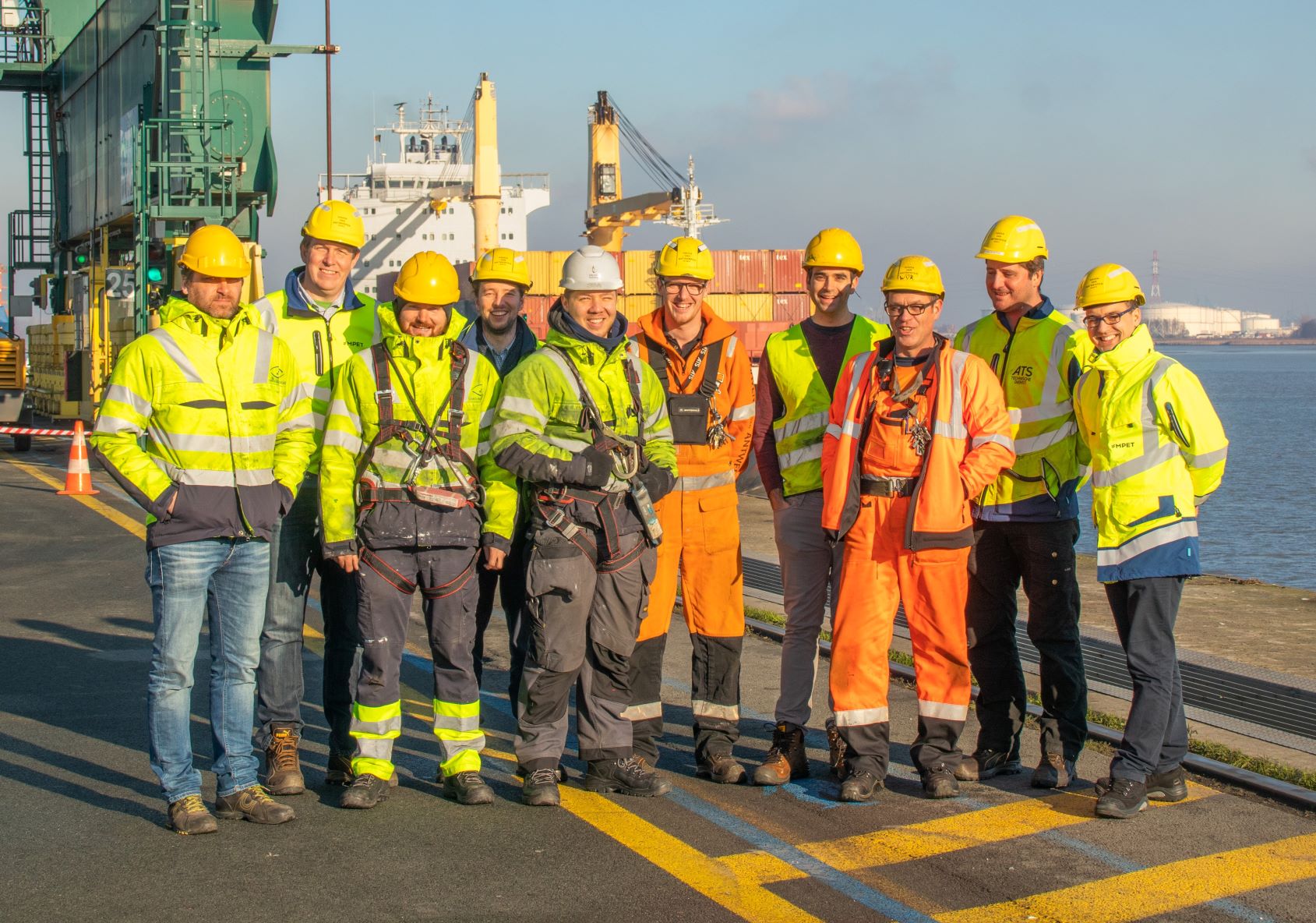
A temporary on-site Camco workshop and specialized MPET STS crane welding and climbing team contributed to speed and agility during installation.
PROTECTING OUR PEOPLE
Safety is built into MPET’s company culture: a lot of effort is put into prevention and supervision of processes. Automation of the tally process enables MPET to have a clearer separation between the man/machine layer. This separation is an important step to prevent accidents from happening.
Automation systems assist the labor force. On the terminals in Antwerp, it is nowadays a challenge to recruit terminal workers. Automation systems at the gates and on the cranes allow motivated, skilled and trained staff to handle the exceptions requiring human interventions. The gang composition can be optimized to handle the work volume. Working smarter, not harder, certainly applies!
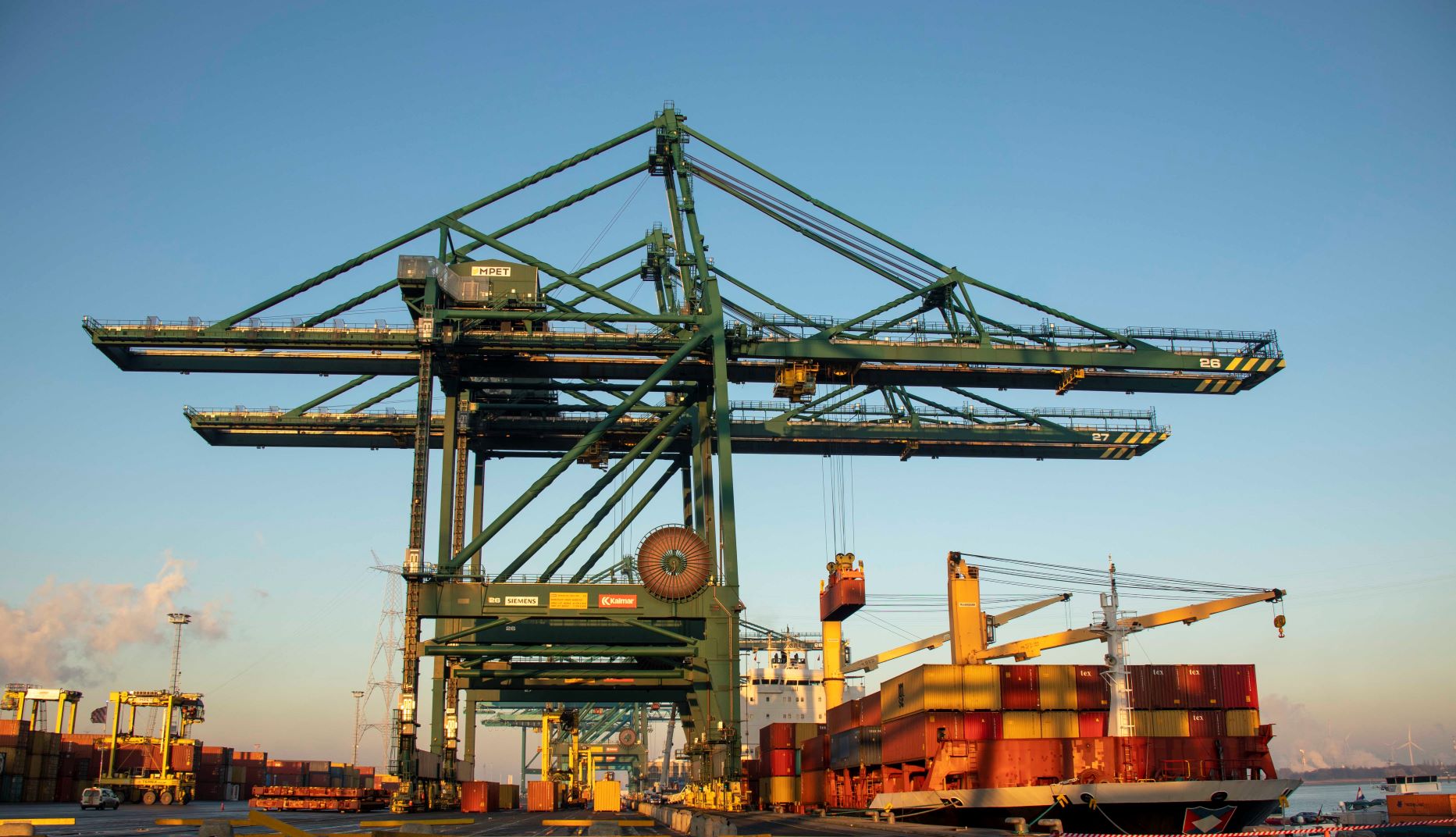
Risk reduction for tally staff, accuracy of information, performance and speed of the processes, overall process quality as well as customer satisfaction.
MPET ANTWERP, BELGIUM
- Capacity: 9 Million TEU/year
- Quay lenght: 3,700m
- Max draft: 17m
- Quay cranes: 41
- Straddle carriers: 234
- Rail handling cranes: 2
- Reefer connections: 2,564
- TOS: Cosmos/TOS
All 41 cranes equipped with Camco BoxCatcher Crane OCR system